Traditional pipeline installation often comes with trade-offs: road closures, lengthy permitting delays, and significant disruptions to surrounding communities. Trenchless construction methods offer a different approach by allowing crews to install underground utilities without disturbing the surface.
Horizontal directional drilling (HDD) and road bores are essential solutions for modern infrastructure challenges. As urban areas grow more congested and permitting becomes more complex, these trenchless solutions help keep critical projects on track. This piece examines how and when these methods are used, the advantages they offer in the field, and how United Pipeline combines them with internal thermoplastic lining to deliver long-term performance, highlighted through a recent road bore installation in Durango, Colorado.
Understanding the Technology: HDD and Road Bores Explained
Trenchless construction has revolutionized the installation of underground utilities, particularly in areas where surface access is limited or disruption must be avoided. Two of the most widely used trenchless methods—horizontal directional drilling (HDD) and road bores—allow crews to install pipelines and conduits beneath the surface without the need for open excavation.
What is Horizontal Directional Drilling (HDD)?
Horizontal directional drilling is a guided, trenchless method used to install pipelines, cables, or conduits beneath obstacles like roads, rivers, and buildings. It’s valued for its precision and ability to reduce surface disruption, making it a preferred choice for both new installations and replacement projects in developed or environmentally sensitive areas.
The HDD process typically unfolds in three phases:
- Pilot Drilling: A small-diameter pilot hole is drilled along a predetermined path using a tracked drill head, guided by electronic locating systems.
- Reaming: The borehole is then enlarged using reaming tools and drilling fluid to remove soil and stabilize the tunnel.
- Product Pipe Pullback: Once the path is prepared, the pipeline or conduit is pulled through the borehole and installed in place.
What is Road Bore?
A road bore is a specific application of HDD used to install utilities beneath roads and highways while keeping the surface fully intact. Rather than excavating across lanes of traffic, crews drill a horizontal path beneath the roadway and pull the pipe or cable through. This approach avoids damage to pavement, eliminates the need for lane closures, and keeps traffic moving, especially important in densely populated or high-traffic areas.
Together, HDD and road bores allow infrastructure teams to complete complex underground installations with greater control and less disruption. Projects benefit from faster timelines and lower surface restoration costs without compromising precision or reliability.
When Trenchless Becomes the Only Option: Navigating Permitting, Infrastructure, and Terrain Challenges
In many infrastructure projects, trenchless methods are the only viable option. Open trenching is often restricted in urban environments where utility congestion, traffic flow, and public safety make surface excavation unworkable.
Permitting constraints are especially common in city centers, under major roadways, and in areas with limited right-of-way access. HDD and road bores allow crews to install new pipelines or replace aging ones without disrupting the surface, helping projects meet regulatory requirements while minimizing community impact.
Trenchless methods are also critical when aging infrastructure needs to be rehabilitated or replaced in place. Steel pipelines running through densely populated areas, for example, may require upgrades that can’t be completed through open-cut methods without disrupting essential services or surrounding systems.
Common use cases include:
- Highway and arterial road crossings
- Protected waterways
- Residential and commercial districts
Case Study: Durango Road Bore + Tite Liner® Installation
A recent project in Durango, Colorado, highlights how trenchless construction and internal pipeline lining can be combined to meet infrastructure demands in sensitive, high-traffic environments.
The goal was to install a new 16-inch steel pipeline beneath an active roadway, without cutting into the pavement or disrupting traffic. Early planning and permitting efforts focused on overcoming surface access limitations and minimizing community impact. With traditional trenching ruled out, a guided horizontal directional drill was selected to complete the road bore safely beneath the corridor.
Once the bore path was confirmed, the team used HDD equipment to install the steel host pipe under the roadway without disturbing the surface. After the pipe was in place, United Pipeline installed its HDPE Tite Liner® to provide internal corrosion protection. The thermoplastic liner was pulled through the steel pipe to create a tight, seamless fit, without the use of adhesives or welding.
This approach enabled the team to meet engineering, permitting, and operational requirements without compromising the project’s pace or integrity—something that wouldn’t have been possible with traditional open-cut methods.
See the Durango installation process in action: Watch the video
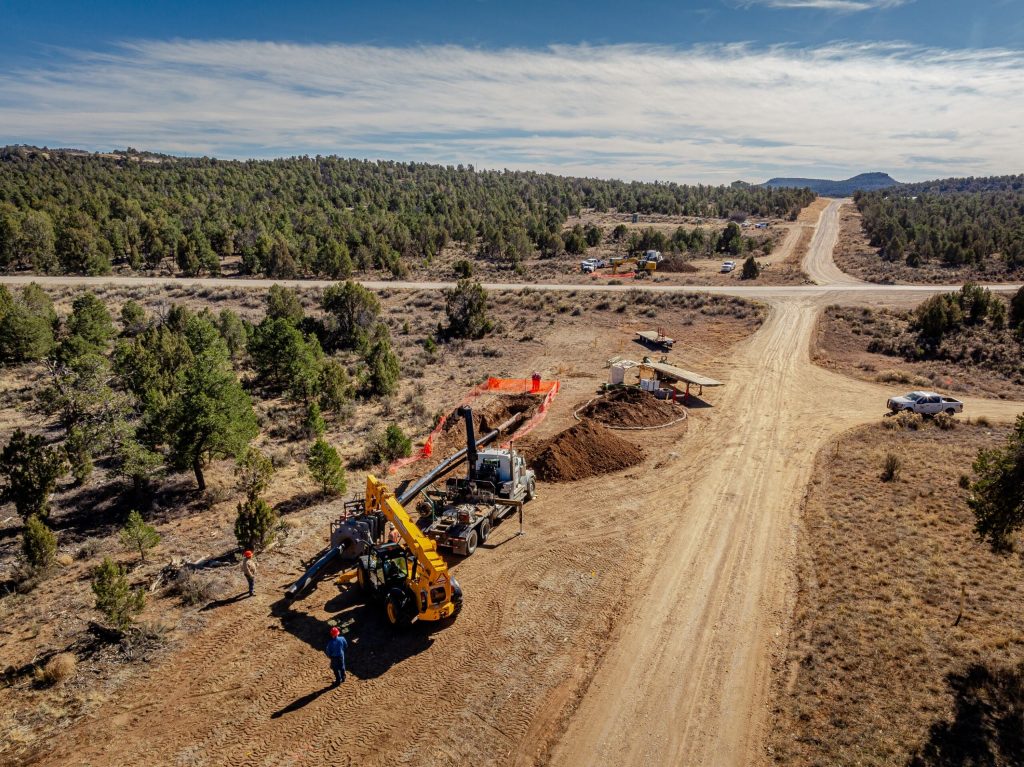
United Pipeline completing a road bore + Tite Liner® project in Durango, Colorado.
Lessons from the Field: Why Trenchless + Lining = Long-Term Value
Projects with limited access, tight working windows, or heavily developed corridors demand more adaptable solutions. Trenchless methods meet those challenges head-on, offering a way to complete underground installations, even in the most constrained environments.
The longer-term value comes from pairing those methods with internal lining systems. With Tite Liner®, new pipelines gain built-in protection against corrosion, and existing pipelines can be rehabilitated without full removal or replacement. The tight-fit design eliminates the need for welding and holds up under aggressive flow conditions, making it ideal for both new construction and infrastructure rehab. That combination reduces future maintenance demands and extends the operating life of critical assets for municipalities, utilities, and private operators alike.
As projects face tighter restrictions on road access and permitting requirements, this integrated approach is increasingly important. United Pipeline brings the experience to execute complex trenchless installations and the proven systems to protect them for decades to come.Ready to talk about your next project? Reach out to learn how trenchless and lining can work together to solve it.