Rotational Lining
Rotational lining (or “rotolining”) is a technology which bonds a uniform, seamless polymer layer to the interior of virtually any metallic structure, regardless of shape and complexity.
This allows for installation in either a mechanical or fully-welded pipe system.
How It Works
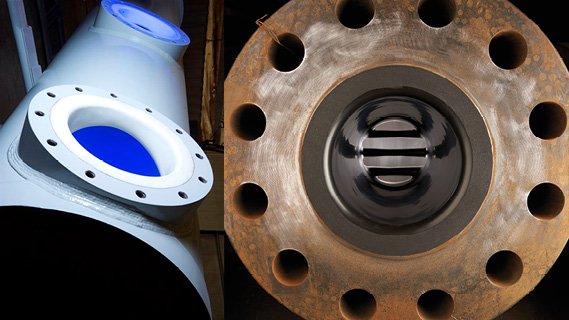
Rotolining Process
In the rotolining process, granular resin is placed inside the structure to be lined and all openings are covered. The structure is heated while simultaneously being rotated about two axis. The resin melts and flows evenly over the entire inner surface of the structure, bonding to the metal substrate.
Once cooled, the result is a monolithic corrosion and chemical resistant lining that conforms to complex shapes and is virtually free of stresses.
Rotolining Success Stories
Rotolining Details & Specs
Fits Many Sizes
We line a wide range of chemical processing, transfer, and storage equipment, including some the largest pipe and vessels in the industry. Our breadth of size and manufacturing capabilities can accommodate most size requirements up to a 6ft diameter x 20ft length, OR 12ft diameter.
Internal Protection
Our state-of-the-art technology uses different high performance thermoplastics to internally protect steel structures, such as:
- Manifolds and well heads
- Tees
- Bends and reducers
High performance
United Pipeline Systems can cover a wide range of fluid requirements, temperatures and applications through the use of high performance thermoplastics such as:
- High Density Polyethylene (HDPE)
- ETFE (Tefzel)
- PFA
- Options: Nylon 12, PVDF (Kynar), ECTFE (Halar)